When it comes to keeping your industrial operations flowing smoothly, few components play as crucial a role as camlock fittings. These unassuming heroes of fluid transfer can make or break your day, depending on how well they’re functioning. But let’s face it – even the best camlock fittings can throw a curveball now and then. That’s why we’re diving deep into the world of troubleshooting common issues with camlock fittings. Whether you’re a seasoned pro or just getting your feet wet in the industrial plumbing game, this guide’s got your back. So, grab your favorite beverage, settle in, and let’s turn those camlock conundrums into a thing of the past!
Table of Contents
The ABCs of Camlock Fittings: Your Crash Course in Fluid Connection Mastery
Before we roll up our sleeves and get into the nitty-gritty of troubleshooting, let’s break down what makes these little marvels tick. Camlock fittings, also known as cam and groove couplings, are the quick-connect superstars of the fluid transfer world. They’re the go-to choice in industries where fast, secure connections are as essential as your morning coffee – think agriculture, manufacturing, chemical processing, and even craft brewing.
Here’s a quick anatomy lesson to get you up to speed:
- Male adapter (plug): The part that slides into the female coupler.
- Female coupler (socket): The receiving end that welcomes the male adapter with open arms.
- Cam arms: These lever-like components are the muscle behind the quick-connect magic.
- Gasket: The unsung hero that creates a tight seal and keeps fluids where they belong.
- Locking pins: Safety first! These pins keep the cam arms from accidentally disengaging.
When you bring these parts together, it’s like watching a perfectly choreographed dance. The male end slides into the female socket, and with a satisfying flip of the cam arms, you’ve got a tight seal faster than you can say “pressure differential.” It’s this elegant simplicity that makes camlocks the darlings of industries where time is money and reliability is non-negotiable.
“In the fast-paced world of fluid transfer, camlock fittings are the equivalent of a firm handshake and a wink – quick, reliable, and always ready for business.” – Sarah Johnson, Industrial Process Engineer
But like any relationship, the one between you and your camlock fittings needs some TLC to stay strong. Let’s dive into the most common issues you might face and how to tackle them head-on.
MORE POST
Starting a Business in Ontario: Your Ultimate 11-Step Checklist
Top 7 Camlock Conundrums (and How to Kick ‘Em to the Curb)
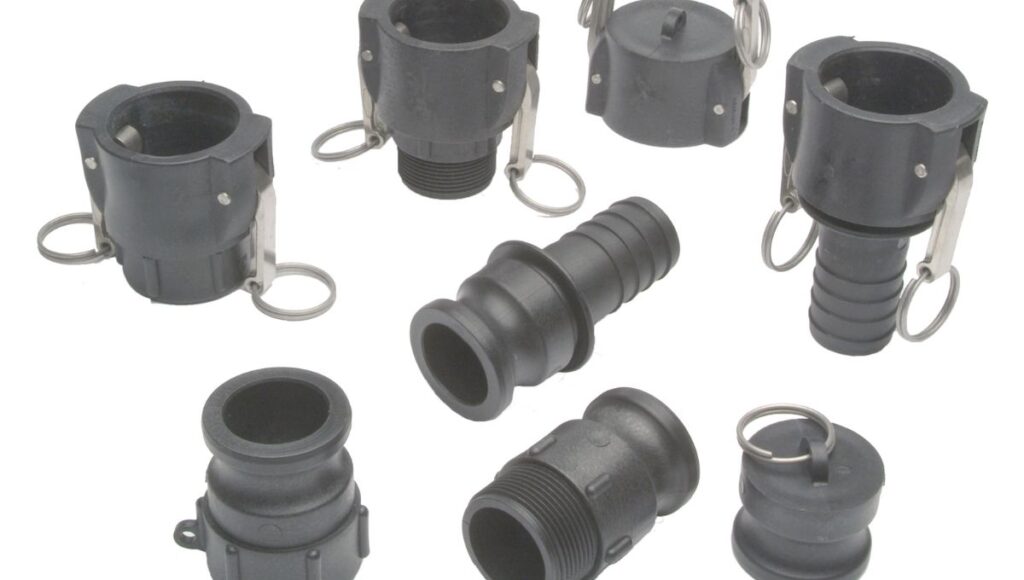
1. Leaky Connections: When Your Fitting Can’t Hold Its Water (or Oil, or Chemicals…)
There’s nothing that’ll ruin your day faster than a camlock fitting that decides to sprinkle your workspace with whatever fluid it’s supposed to be containing. Leaks are the bane of any operator’s existence, but fear not – we’ve got some tricks up our sleeve to keep things dry and dandy.
Troubleshooting tips:
- Check the gasket: This rubber ring is your first line of defense against leaks. If it’s looking worse for wear – cracked, deformed, or just plain old – it’s time for a replacement. Pro tip: Always keep a stash of spare gaskets on hand. You’ll thank yourself later.
- Ensure full engagement: Those cam arms aren’t just for show. Make sure they’re fully flipped and locked into place. Halfway doesn’t cut it when you’re dealing with pressurized fluids.
- Inspect for damage: Give your fittings a once-over for any signs of wear, dents, or scratches. Even small imperfections can lead to big leaks.
- Clean sealing surfaces: Sometimes, a bit of gunk is all it takes to compromise your seal. Give those surfaces a good wipe-down before connection.
2. Stubborn Couplings: Wrestling with Connections and Disconnections
When your camlock fittings decide to play hard to get, it’s time to show ’em who’s boss. Difficulty in connecting or disconnecting is a common headache, but we’ve got the aspirin – and it doesn’t involve a sledgehammer (tempting as that might be).
Troubleshooting tips:
- Clean both ends: Dirt and debris are the arch-nemeses of smooth connections. A quick clean can work wonders.
- Check for misalignment: Sometimes, all you need is a gentle nudge to get things lined up just right.
- Lubricate moving parts: A little food-grade lubricant can go a long way in keeping things moving smoothly. Just make sure it’s compatible with your transferred fluids.
- Inspect for damage: Bent cam arms or warped fittings can make connections a nightmare. If you spot damage, it might be time for a replacement.
3. Rust Monsters Attack: Battling Corrosion and Rust
Rust never sleeps, and it’s got a particular taste for camlock fittings. But with the right moves, you can keep these metal-munching monsters at bay and ensure your fittings stay rust-free and ready for action.
Troubleshooting tips:
- Choose wisely: Opt for corrosion-resistant materials like stainless steel or aluminum when possible. Your future self will thank you.
- Regular cleaning is key: Don’t let your fittings marinate in harsh chemicals or moisture. A quick wipe-down after use can prevent a world of rust-related hurt.
- Consider protective coatings: For extra defense in harsh environments, look into specialized coatings that can give your fittings an extra layer of protection.
- Store smart: Keep your fittings in a dry environment when not in use. Moisture is rust’s best friend, so don’t invite it to the party.
4. Worn-out Warriors: Dealing with Seal Surface Fatigue
Even the toughest camlock fittings can get battle-weary. When sealing surfaces start to show their age, it’s time for some TLC to keep your connections tight and your fluids where they belong.
Troubleshooting tips:
- Regular inspections: Make it a habit to give your fittings a good once-over on a regular basis. Look for signs of wear, pitting, or scoring on the sealing surfaces.
- Proactive replacement: Don’t wait for a leak to tell you it’s time for new parts. If you spot significant wear, replace components before they cause a full-blown failure.
- Material matters: Use gaskets that are compatible with your transferred fluids. The right material can significantly reduce wear and extend the life of your fittings.
- Proper alignment: Ensure your fittings are always properly aligned during connection. Misalignment can cause uneven wear and premature failure.
5. Storage Snafus: Keeping Your Camlocks Happy Between Gigs
Proper storage isn’t just about keeping your workspace tidy – it’s about extending the life of your fittings and ensuring they’re ready to perform when duty calls. Treat ’em right when they’re off-duty, and they’ll have your back when it’s go-time.
Troubleshooting tips:
- Clean and dry: Before storage, give your fittings a thorough cleaning and make sure they’re completely dry. Moisture is the enemy of longevity.
- Use protective caps: Invest in some protective caps or plugs to keep dirt, dust, and debris out of your fittings during downtime.
- Organize with care: Store your fittings in a way that prevents them from banging against each other. A little organization goes a long way in preventing scratches and dents.
- Climate control: If possible, store your fittings in a climate-controlled environment to prevent temperature-related stress and condensation.
6. Hulk-Mode Mishaps: The Perils of Over-Tightening
We get it – you want a tight seal. But there’s a fine line between secure and squashed. Over-tightening can turn your camlock fitting into a paperweight faster than you can say “oops.”
Troubleshooting tips:
- Follow the specs: Manufacturers provide torque specifications for a reason. Follow them religiously to avoid the temptation of over-tightening.
- Use proper tools: The right tools can help you avoid Hulk-smashing your fittings. Invest in quality wrenches and consider using a torque wrench for critical applications.
- Train your team: Make sure everyone who handles camlock fittings understands the importance of proper tightening techniques. A little education can save a lot of headaches.
- Visual indicators: Some modern camlock fittings come with visual indicators to show when they’re properly tightened. If you’ve got ’em, use ’em!
7. Size Matters: Picking the Right Camlock for the Job
Using the wrong size fitting is like trying to fit a square peg in a round hole – it’s not gonna end well, and you might end up with a mess on your hands (and floor… and walls…).
Troubleshooting tips:
- Double-check specs: Always, always, always verify the specifications before ordering or installing new fittings. A little due diligence goes a long way.
- Consult the experts: When in doubt, reach out to suppliers or manufacturers. They’re usually more than happy to help you find the right fit for your application.
- Standardize where possible: Try to standardize fittings across your operation to reduce the risk of mix-ups. It’ll make inventory management easier, too.
- Label clearly: If you’re working with multiple sizes, implement a clear labeling system to prevent confusion on the job.
Camlock Care 101: Keeping Your Fittings Fighting Fit
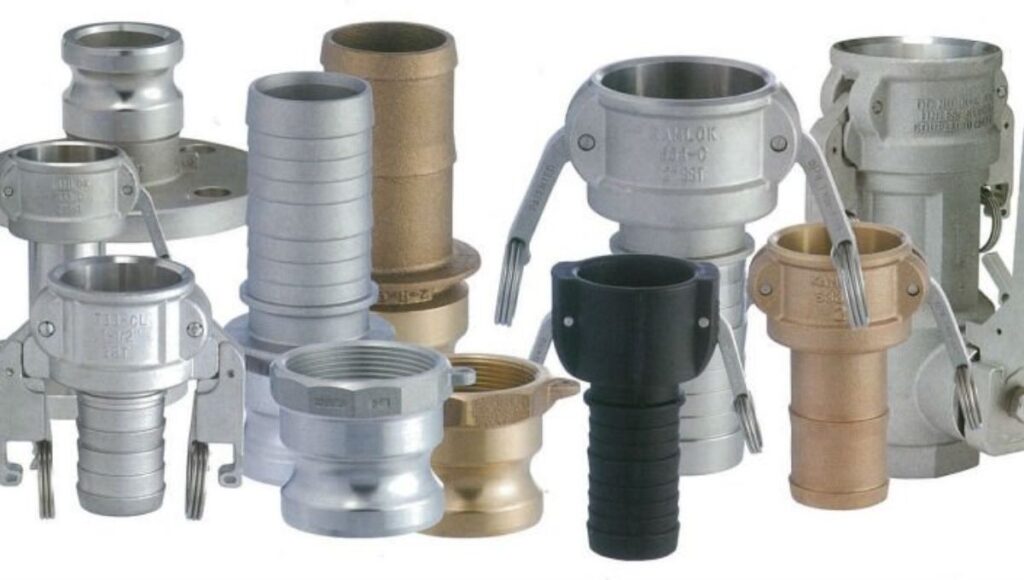
An ounce of prevention is worth a pound of cure, especially when it comes to camlock fittings. Implementing a solid maintenance routine can save you time, money, and a whole lot of frustration down the line. Here’s a handy table to keep your camlocks in tip-top shape:
Maintenance Task | Frequency | Why It Matters | Pro Tips |
Visual Inspection | Daily | Catch small issues before they become big problems | Look for signs of wear, damage, or corrosion |
Cleaning | After each use | Prevent build-up of residue and contaminants | Use appropriate cleaning solutions for your application |
Lubrication | Monthly | Keep moving parts smooth and reduce wear | Use food-grade lubricants for food and beverage applications |
Full Disassembly & Cleaning | Quarterly | Deep clean and thorough inspection | Great opportunity to replace worn gaskets or O-rings |
Gasket Replacement | As needed or annually | Ensure a tight seal and prevent leaks | Keep a stock of common gasket sizes on hand |
Pressure Testing | Bi-annually | Verify system integrity and catch potential leaks | Follow industry standards for pressure testing procedures |
a well-maintained camlock fitting is a happy camlock fitting. By sticking to a regular maintenance schedule, you’ll not only extend the life of your fittings but also reduce the likelihood of unexpected failures and downtime.
When DIY Won’t Cut It: Knowing When to Call in the Pros
As much as we all love a good DIY project, there comes a time when you’ve got to know when to fold ’em and call in the cavalry. Here are some red flags that scream “expert needed!”:
- Severe corrosion or damage to the fitting body
- Stripped or damaged threads
- Persistent leaks despite your best troubleshooting efforts
- Any modification needed to meet specific regulations or certifications
- Unusual wear patterns that you can’t explain
- Fittings exposed to extreme conditions outside their normal operating parameters
When these issues pop up, it’s time to ring up a camlock whisperer (aka a professional technician). They’ve got the specialized tools, expertise, and access to parts that can tackle even the toughest camlock conundrums.
Case Study: The Midnight Meltdown
Picture this: It’s 2 AM at a busy chemical processing plant. A critical transfer line starts leaking at a camlock fitting, threatening to shut down production and cause a safety hazard. The on-site team tries every trick in the book, but the leak persists. That’s when they call in Marco, the local camlock guru.
Marco arrives, takes one look at the fitting, and spots the issue – a hairline crack in the female coupler, invisible to the untrained eye. With a specialized tool and a replacement part from his van, he has the line back up and running in 30 minutes flat. The moral of the story? Sometimes, the cost of downtime far outweighs the cost of calling in an expert.
Camlock Crystal Ball: Future-proofing Your Fitting Game
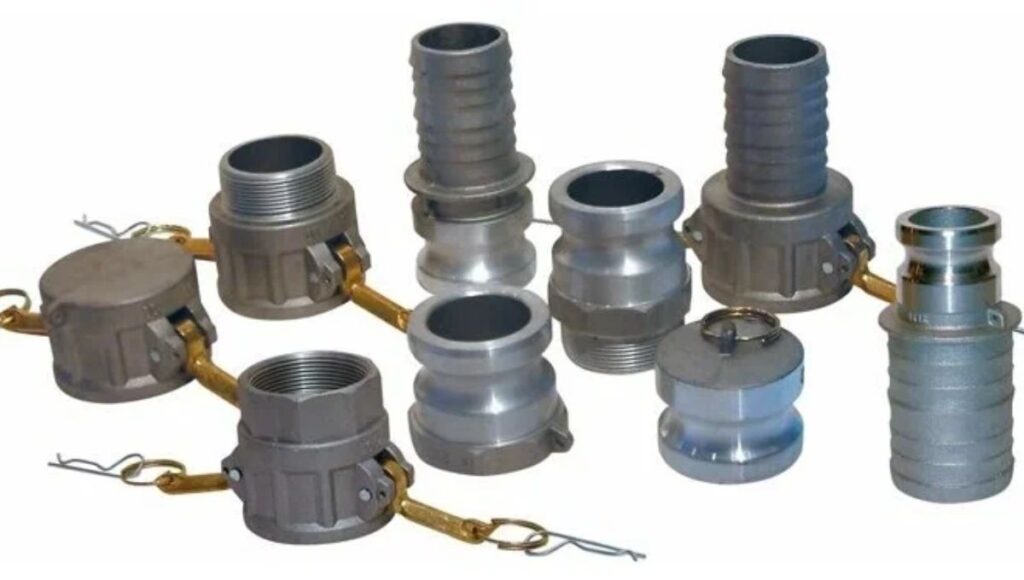
The world of camlock fittings isn’t standing still, and neither should you. Staying ahead of the curve can give you a serious edge in efficiency and reliability. Here’s what’s on the horizon:
- Smart fittings with embedded sensors to detect leaks, wear, and even flow rates
- Eco-friendly materials for the environmentally conscious operator
- Enhanced coatings for even better corrosion resistance and longer life
- RFID-enabled fittings for easy tracking and maintenance scheduling
- Self-aligning designs to reduce connection errors and improve efficiency
To stay ahead of the game and future-proof your fitting setup, consider these tips:
- Keep an eye on industry publications and websites for news about emerging camlock technologies
- Attend trade shows and industry conferences to see the latest camlock tech in action
- Invest in ongoing training for your team to keep their skills sharp and up-to-date
- Build relationships with suppliers who can keep you informed about new products and innovations
- Consider participating in beta testing programs for new camlock technologies
The goal isn’t just to solve today’s problems, but to anticipate and prevent tomorrow’s issues before they even arise.
Wrapping It Up: Your Camlock Cheat Sheet
We’ve covered a lot of ground, so let’s bring it home with a quick-fire recap of our top troubleshooting tips for common camlock fitting issues:
- Leaks? Check gaskets, ensure full engagement, and inspect for damage.
- Stubborn connections? Clean thoroughly, check alignment, and lubricate if necessary.
- Rust rearing its ugly head? Choose resistant materials, clean regularly, and store properly.
- Wear and tear getting you down? Inspect often, replace worn parts proactively, and use compatible materials.
- Storage woes? Keep ’em clean, dry, and protected when not in use.
- Over-tightening temptations? Follow manufacturer specs and use proper tools.
- Size issues throwing you for a loop? Double-check before you buy or install, and standardize where possible.
conclusion:
Tackling common camlock fitting issues boils down to seven key points: address leaks promptly, ease stubborn connections, fight rust, manage wear and tear, store properly, avoid over-tightening, and use the right size. Regular maintenance is crucial for keeping your fittings in top shape. When faced with severe problems, don’t hesitate to call in the experts. Stay ahead of the game by keeping an eye on emerging technologies in the camlock world. well-maintained camlock fittings are essential for smooth operations. By following these tips and staying vigilant, you’ll ensure your fluid transfer systems run efficiently and reliably. Share your experiences and keep learning from the camlock community!